Melting
Raw material is split into magnesium and aluminum alloys. For all materials uniform melting methods are applied facilitated by regular furnace cleaning intervalls to ensure cleanliness of the liquid. The appropriate alloy composition is crucial to ensure proper casting conditions to reach the required quality level.
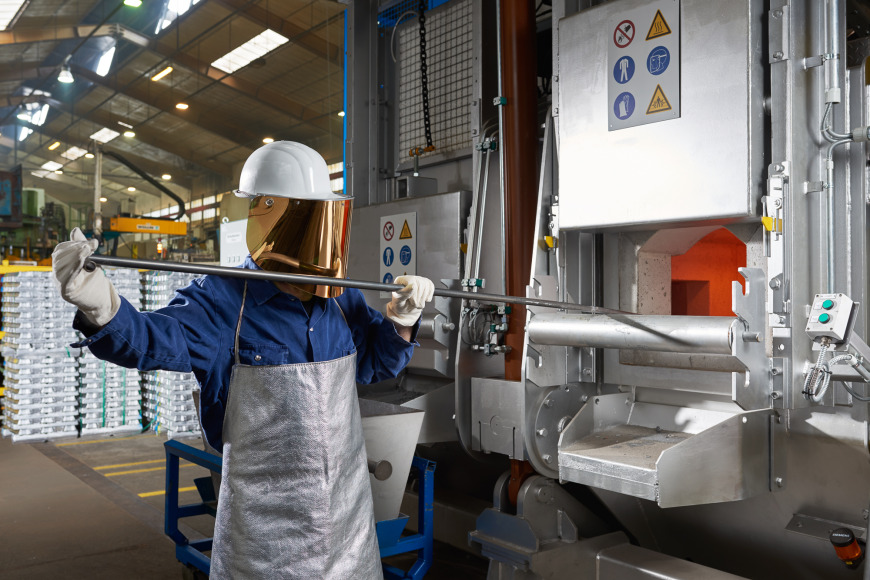
Process
Magnesium is melted electrically directly at the die casting cell. From the multi-chamber furnaces with separate melting and dosing chambers magnesium is poured into the casting chamber through pumping. This is due to the reactivity of the liquid magnesium under protective gas and ensures compliance with the highest safety standards for equipment and operators.
Alloys
Aluminum
|
Magnesium
|
---|---|
226 - AlSi9Cu3(Fe)Z
|
AZ91
|
230 - AlSi12
|
AMZ40
|
231 - AlSi12(Cu)
|
AM50
|
239 - AlSi10Mg(Fe)
| |
Structural casting - AlSi10MnMgSr
|